La trasformazione digitale nelle PMI manifatturiere in Italia
Quello che stiamo vivendo è potenzialmente un periodo d’oro per le piccole e medie imprese manifatturiere italiane. Le tecnologie digitali possono dare una marcia in più anche (e soprattutto) alle aziende più piccole, che possono affrontare più agilmente di realtà più grandi e complesse un processo di trasformazione digitale in grado di proiettarle in breve tempo a giocare in un campionato diverso dal proprio mercato tradizionale, confrontandosi direttamente con grandi aziende internazionali.
Ma le aziende manifatturiere nostrane hanno la percezione di ciò? Come stanno affrontando il tema della trasformazione digitale nel proprio settore, tra digital manufacturing e Industria 4.0? Quali sono gli obiettivi che si pongono e quali le loro priorità?
Questi e altri temi sono stati oggetto di una ricerca promossa da SAP e dal DEVO Lab (Digital Enterprise Value and Organization), un centro di ricerca della SDA School of Management Bocconi coordinato da Gianluca Salviotti, Professore di Information Systems e Digital Transformation in SDA Bocconi.
La ricerca ha interessato un campione di circa 1.200 PMI italiane rappresentative del settore manifatturiero e si è concentrata in particolare sul digital manufacturing, ovvero la digitalizzazione degli impianti produttivi, che è solo uno degli aspetti che compongono l’ecosistema della Industry 4.0.
Introducendo il tema, il professor Salviotti ha evidenziato il fatto che la digitalizzazione sta permeando l’industria manufatturiera da due diverse direttrici, in qualche caso convergenti:
- La digitalizzazione del prodotto. Il manufatto ha a bordo sempre più sensori e componenti che generano dati digitali e che, una volta collegati, abilitano una nuova generazione di servizi;
- La digitalizzazione del processo produttivo. L’analisi dei dati provenienti dai sensori a bordo macchina, correlati ai fattori più diversi, porta a migliorare l’efficienza e ad ottimizzare la manutenzione. La robotica avanzata permette una produzione sempre più personalizzata sulle scelte del cliente. Il tutto trasforma non solo l’impianto produttivo, ma l’intera gestione aziendale.
La trasformazione digitale vera e propria avviene nell’intersezione tra le due aree, attraverso l’integrazione di queste informazioni in tutte le aree di business, per cambiare in modo fondamentale il modo in cui l’azienda opera e il valore che trasferisce al cliente.
Commentando la ricerca, la COO di SAP Italia Carla Masperi ha affermato che l’Italia ricopre un ruolo molto importante per SAP, perché è la seconda potenza manifatturiera europea, ed è fondamentale per l’azienda poter accompagnare le aziende italiane in un percorso di digitalizzazione. Probabilmente non è a caso che SAP abbia scelto a livello globale un nome italiano, Leonardo, per la sua piattaforma che integra i dati provenienti dai dispositivi IoT nel sistema ERP aziendale.
Trasformazione digitale e Industry 4.0 sono temi che gli imprenditori affrontano con consapevolezza e maturità, e non solo per gli incentivi previsti dal piano Calenda, che rappresenteranno un acceleratore importante ma che non saranno per tutti. Per via del timing molto ristretto solo le aziende già sensibili e al lavoro sul tema potranno cogliere appieno le opportunità, e la modalità del superammortamento porterà vantaggi solo ad aziende che sono già profittevoli
Per Masperi, la digitalizzazione permette di accorciare le distanze tra piccola e grande azienda. Attraverso il cloud e i business network le PMI riescono a raggiungere una scala globale in tempi velocissimi, arrivando a competere con i player più grandi in tempi molto rapidi.
Lo stato del digital manufacturing in Italia
Secondo i risultati, il tema è sentito con forza dalle PMI. In particolare, il 27% delle aziende interpellate ha già completato una primo progetto di digitalizzazione, il 36% ha un progetto in corso e il 13% ha dichiarato l’intenzione di farlo entro il 2017. La sensibilità al tema e la priorità si misurano, pragmaticamente, osservando come vengono allocati i budget e quali sono le figure investite della responsabilità dei progetti digital.
Trasformazione digitale: da dove viene il budget e chi ne è responsabile
Nel 65% dei casi analizzati i progetti di digitalizzazione hanno un budget stanziato direttamente dalla direzione centrale, mentre nell’11% dei casi ogni divisione dispone di un suo budget specifico per il digitale.
Questo orientamento a un presidio centrale del tema emerge anche dalle figure incaricate dei progetti di trasformazione digitale. Emerge un ruolo centrale del Responsabile dei Sistemi Informativi (indicato nel 48% dei casi in una domanda che ammetteva risposte multiple), ma anche questa figura è sovrastata dalla somma data dal coinvolgimento della prima linea manageriale (CEO o Direttore Generale, 40%) e della Proprietà (36%). Il 47% delle aziende distribuisce comunque la responsabilità della digitalizzazione su più persone e funzioni, creando una sorta di comitato.
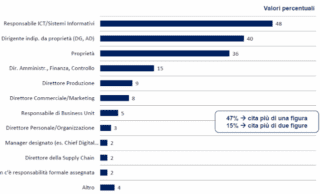
Le figure in azienda investite della responsabilità dei progetti di trasformazione digitale. il 47% delle aziende più di una figura, il 15% più di due.
Poco diffusa è la figura dirigenziale specializzata nel digital (il cosiddetto CDO), che sta invece emergendo in aziende più grandi o al di fuori del settore manifatturiero.
Digitalizzazione: obiettivi e speranze delle aziende
Tra i motivi che spingono le aziende ad affrontare la digitalizzazione, emerge un focus principalmente sui fattori interni all’azienda: migliorare l’efficienza e la produttività (57%), ottenere benefici in termini di coordinamento interno (47%) e migliorare la qualità (33%). Secondo il professor Salviotti, questa non deve necessariamente essere vista come una mossa difensiva: spesso questo è un passaggio preparatorio necessario per poter poi affrontare la trasformazione in modo più radicale, rivolgendo questa volta lo sguardo all’esterno dell’azienda.
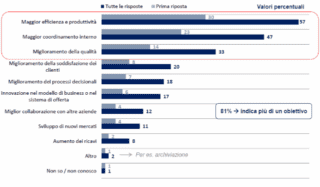
Gli obiettivi della trasformazione digitale per le imprese manufatturiere italiane. I primi tre valori corrispondono a un focus tutto interno all’azienda.
Cloud Computing e Robotica avanzata sono le tecnologie da cui le aziende si aspettano un impatto più radicale sull’industria, mentre stampa 3D e realtà aumentata quelle da cui le aziende si aspettano un minore impatto sul proprio business. Va detto però che nel mondo manufatturiero la stampa 3D, sebbene con tecnologie diverse, è un fenomeno già consolidato da decenni: le aziende che dovevano valutare la sua adozione, lo hanno già fatto, anche se per finalità più tradizionali, come la prototipazione o la creazione di stampi da portare poi in produzione con altre tecniche.
I CIO stanno investendo principalmente nel cloud computing, per un 59% complessivo suddiviso in soluzioni Infrastructure as a Service, Software as a Service e Platorm as a Service, seguito da sicurezza (30%), tecnologie di integrazione (24%), tecnologie Big Data (16%) e In-memory computing (11%).
Le conseguenze della digitalizzazione su occupazione e risorse umane
Sul fronte dell’occupazione, i responsabili HR non prevedono un impatto negativo della digitalizzazione sul numero di impiegati, ma indicano che saranno necessari sforzi per la riqualificazione del personale e soprattutto un maggior livello di coordinamento tra i reparti.
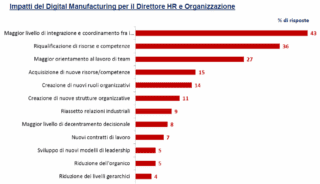
Gli impatti della trasformazione digitale sulla forza lavoro viste dai responsabili delle risorse umane e organizzazione.
Dopo anni in cui la produzione è stata spostata all’estero, inseguendo risparmi sul fronte della mano d’opera, dell’energia e normative meno stringenti, si sta assistendo al fenomeno del reshoring, ovvero il ritorno in patria degli impianti produttivi.
La sofisticazione tecnologica richiede infatti lavoratori più qualificati, e la produzione personalizzata in base alle scelte del cliente finale non può permettersi i lunghi tempi di una spedizione navale da continenti lontani. Nei primi 6 mesi del 2016 sono state 120 le aziende italiane ad aver ri-localizzato il personale, il 10% delle quali nel settore manifatturiero, ha commentato Carla Masperi.