Industria 4.0: Italia, sicurezza, normative e best practice
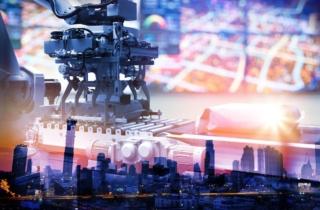
In un articolo di approfondimento, Kaspersky ha voluto fare il punto sull’Industria 4.0, termine usato per la prima volta nel corso della Fiera di Hannover nel 2011. Da quel giorno la “quarta rivoluzione industriale” della nostra storia ha determinato e continua a portare con sé cambiamenti radicali nei processi produttivi, nelle professionalità e nelle abilità richieste, così come nell’assetto generale degli impianti di produzione e nei modelli di organizzazione. Il quadro evolutivo è in pieno sviluppo e le iniziative che si metteranno in atto nei prossimi anni saranno cruciali per definire l’evoluzione dei processi e il loro impatto sul mondo.
Dal mondo dell’Industrial Internet of Things (le tecnologie basate su smart objects e reti intelligenti) all’Industrial Analytics (in grado di sfruttare le informazioni celate nei big data), fino al Cloud Manufacturing (l’applicazione in ambito manifatturiero del cloud computing). E ancora tutto l’universo dell’Advanced Automation (le tecnologie affini alla robotica), l’Advanced Human Machine Interface (HMI, i dispositivi indossabili e le nuove interfacce uomo/macchina) o l’Additive Manufacturing fanno parte di questo grande macrocosmo tecnologico-industriale.
La Germania è considerata tra i pionieri dell’Industria 4.0 in Europa, seguita dalla Francia, che si è dotata rapidamente di una serie di misure per incentivare le aziende ad allinearsi alla quarta rivoluzione industriale. Negli Stati Uniti, invece, l’approccio al fenomeno ha forme diverse da quelle europee ma analoghi obiettivi. E in Italia? Uno degli studi più recenti, EY Manufacturing Lab 2019, mostra come le aziende italiane debbano ancora fare dei passi in avanti nel pieno accoglimento di un approccio 4.0, anche se una buona parte sta già gettando le basi per una corretta gestione digitale dei processi.
Oltre a gli indubbi aspetti positivi portati dall’Industria 4.0, vanno però sottolineati anche quelli negativi, o potenzialmente tali. La convergenza tra mondo IT e OT, la maggior connettività alle reti esterne e il crescente numero di dispositivi IoT ad uso industriale (IIoT) determinano infatti un aumento del livello di rischio e un’esposizione alle cyberminacce davvero preoccupante se si considerano le possibili conseguenze: danni ai prodotti, opportunità commerciali perse, perdita di fiducia nei confronti di un’azienda, problematiche a livello ambientale, cali nella produzione e molto altro ancora.
La direttiva NIS
Questo scenario ha portato a una riflessione a livello internazionale e all’adozione da parte del Parlamento Europeo, nel 2016, della direttiva sulla sicurezza dei sistemi delle reti e dell’informazione, NIS (Network and Information Security), il cui obiettivo principale era raggiungere un livello elevato di sicurezza dei sistemi, delle reti e delle informazioni comune a tutti i Paesi membri dell’UE.
Anche l’Italia, con il Decreto Legislativo del 18 maggio 2018, ha dato attuazione alla Direttiva, che non ha un orientamento prescrittivo ma indica gli obiettivi da raggiungere, lasciando ai singoli soggetti ampio margine di manovra nell’individuare e implementare mezzi e strumenti considerati idonei per il loro raggiungimento. Al di là della Direttiva sovranazionale, rimane comunque fondamentale avere una corretta conoscenza dello scenario generale, delle cyberminacce in ambito industriale, così come delle best practice da mettere in atto per una maggiore protezione di processi e sistemi.
Il 2019 è stato l’anno della digitalizzazione dell’automazione OT
L’esito dell’analisi condotta nel 2019 da Kaspersky sullo stato della sicurezza informatica dei sistemi di controllo industriale (ICS), nonché sulle priorità, le preoccupazioni e le sfide che comporta, ha evidenziato la natura evolutiva delle minacce, le principali preoccupazioni delle aziende in caso di incidente informatico agli ICS e il tipo di risposta messa in campo dalle organizzazioni industriali.
Secondo il report, il 2019 è stato l’anno della digitalizzazione dell’automazione OT, una tendenza che implica una serie di riflessioni, a partire dalla natura stessa di questo tipo di sistemi. L’automazione OT porta ad un aumento delle connessioni a Internet, questo tipo di reti stanno diventando sempre più sofisticate e il numero degli attacchi continuerà ad aumentare. La conformità alle best practice e agli standard generali della cybersecurity sarà sempre più importante, ma considerando la mancanza di esperti di sicurezza informatica in ambito OT/ICS e il rischio crescente di attacchi sempre più pericolosi, l’implementazione di nuove soluzioni di cybersecurity è ampiamente consigliata.
Per affrontare le sfide attuali e future in ambito industriale, il consiglio di Kaspersky è quello di adeguare le proprie strategie, comprese le decisioni relative al personale, al budget e alle tecnologie necessarie. Un insieme di soluzioni di cybersecurity adatte alle specifiche esigenze e una policy chiara dovrebbero aiutare le realtà industriali di qualunque dimensione a raggiungere il livello di protezione necessario e richiesto anche dalle normative.
Queste soluzioni dovrebbero contenere funzionalità “technology-oriented” e garantire una protezione comprovata contro gli attacchi informatici per ogni singola tipologia di realtà industriale, senza compromettere la business continuity. Dovrebbero avere funzioni di valutazione delle vulnerabilità e misure di Incident Response, offrendo una protezione completa, persino dalle minacce sconosciute più avanzate. Senza dimenticare le iniziative di formazione per il personale, fondamentali per tutti i dipendenti che lavorano con i sistemi di automazione industriali.