5 casi d’uso per l’Edge Computing
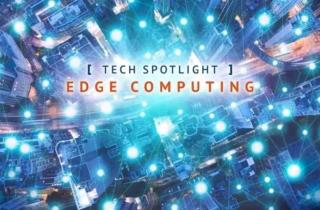
Macchine minerarie autonome e sicure, anche senza connessione di rete
I tecnici di Boliden in questo momento stanno estraendo rame, zinco, piombo, oro e argento. Ma lo stanno facendo comodamente da una sala di controllo fuori terra piuttosto che da tunnel centinaia di metri sotto la superficie.
Presso il sito di Boliden a Garpenberg, in Svezia, le attrezzature minerarie autonome operano in aree che potrebbero essere pericolose per la presenza di persone. Saturo di polveri e soggetto a infiltrazioni d’acqua, gas tossici e vibrazioni, l’ambiente delle miniere è inospitale anche per i dispositivi di comunicazione.
L’automazione ha trasformato l’industria mineraria ormai da molti anni. Il fornitore di macchinari minerari Sandvik Mining and Rock Technology ha prodotto la sua prima attrezzatura autonoma già nel 2004. Lo stato dell’arte oggi è una flotta di attrezzature completamente autonoma che funziona in una miniera sotterranea. “I computer di bordo controllano le macchine in modo indipendente, senza che sia necessaria alcuna interazione umana”, afferma Petri Mannonen, responsabile della linea di prodotti per la gestione delle informazioni minerarie presso Sandvik, che fornisce attrezzature e servizi per lavori quali perforazione della roccia, frantumazione e vagliatura, carico e alaggio, scavo e demolizione.
Il principale motore della modernizzazione delle miniere è la sicurezza dei dipendenti. “L’estrazione sotterranea è un ambiente pericoloso. Allontanare le persone da quell’ambiente pericoloso aumenta la sicurezza”, afferma Mannonen.
Migliorare l’efficienza operativa è un altro obiettivo chiave.
Con l’avanzare della tecnologia mineraria, sono aumentati anche i requisiti per la connettività di rete. Il punto non è riuscire a connettere un laptop, ma tutti i macchinari connessi alla rete che sono fondamentali per le operazioni. Man mano che le miniere diventano più intelligenti, le compagnie minerarie stanno estendendo la connettività da piccole reti dedicate a reti a livello di miniera. Con una connettività più pervasiva, le società minerarie possono utilizzare il rilevamento di prossimità per mantenere tutte le persone, le attrezzature e altre risorse a distanza di sicurezza. In caso di emergenza, una connettività più affidabile può aiutare a coordinare le comunicazioni e i soccorsi.
Presso il sito di Garpenberg di Boliden, Sandvik fornisce l’attrezzatura mineraria insieme al software operativo, basato sulle tecnologie di rete Industrial IoT di Cisco, per connessioni cablate e wireless. Il software AutoMine di Sandvik consente il controllo autonomo delle attrezzature minerarie sotterranee e il controllo remoto in modo che, nella sala di controllo in superficie, gli ingegneri minerari possano tenere traccia delle risorse e apportare le modifiche necessarie. Boliden utilizza anche il software OptiMine di Sandvik, che raccoglie i dati dall’attrezzatura mineraria e li analizza per ottimizzare la produzione.
Sul lato rete, Boliden gestisce una rete IoT a bassa latenza utilizzando switch industriali e punti di accesso Cisco. Mantenere la rete connessa nel sottosuolo è imperativo. “Per poter garantire che l’ambiente e le macchine funzionino in sicurezza, è davvero indispensabile avere una rete di comunicazione robusta e affidabile, che garantisca continuità dall’apparecchiatura fino alla sala di controllo, passando per le soluzioni di sicurezza”, afferma Mannonen.
Questa connettività ha contribuito a trasformare le operazioni minerarie in generale e il modello di business di Sandvik, afferma Dave Wilson, President of Global Sales IoT di Cisco: “Possono rendere i loro veicoli più intelligenti. Possono avere diversi pezzi – strumenti, sensori e software – che consentono di trasformare il loro veicolo in un unico grande sensore che analizza cosa sta succedendo, ottimizzando l’intero processo”.
L’installazione presso la miniera di Garpenberg, un chilometro e mezzo sotto terra, consente agli ingegneri minerari di monitorare le persone e le attrezzature in tempo reale. I sensori di bordo vengono utilizzati per scopi di navigazione e per monitorare lo stato di salute dell’apparecchiatura, assicurandosi che tutto funzioni a livelli ottimali. I dati raccolti dalle miniere informano anche le decisioni operative, semplificando la pianificazione.
È una soluzione in grado di trasformare le operazioni minerarie. Un camion autonomo lavorare senza stancarsi, con una precisione fino al centimetro, raggiungendo posti da cui non saremmo ma stati in grado di estrarre prima. E grazie all’elaborazione e all’analisi eseguita in loco, può funzionare in aree della miniera che non sono ancora state raggiunte dalla rete.
- Pagina principale
- La IA nell’Edge velocizza la manutenzione dei treni merci
- Analisi dei dati nella produzione di fiale per medicinali e vaccini
- Tutti i servizi dell’albergo in un’app sensibile al contesto
- Infrastrututture Edge HCI per i negozi di alimentari
- Macchine minerarie autonome e sicure, anche senza connessione di rete